Partner: HEGAs s.r.o.
Field: Power Engineering
The HEGAs company from Třinec, a specialist in innovations in small-scale energy, has set itself the goal of developing a heat exchanger to efficiently use flue gas heat that would otherwise not be used. In their development, they are cooperating with BENEKOV and VSB-TUO.
This process requires precise technical calculations, which are key to meeting technical and economic requirements. Traditional computational methods are already reaching their limits.
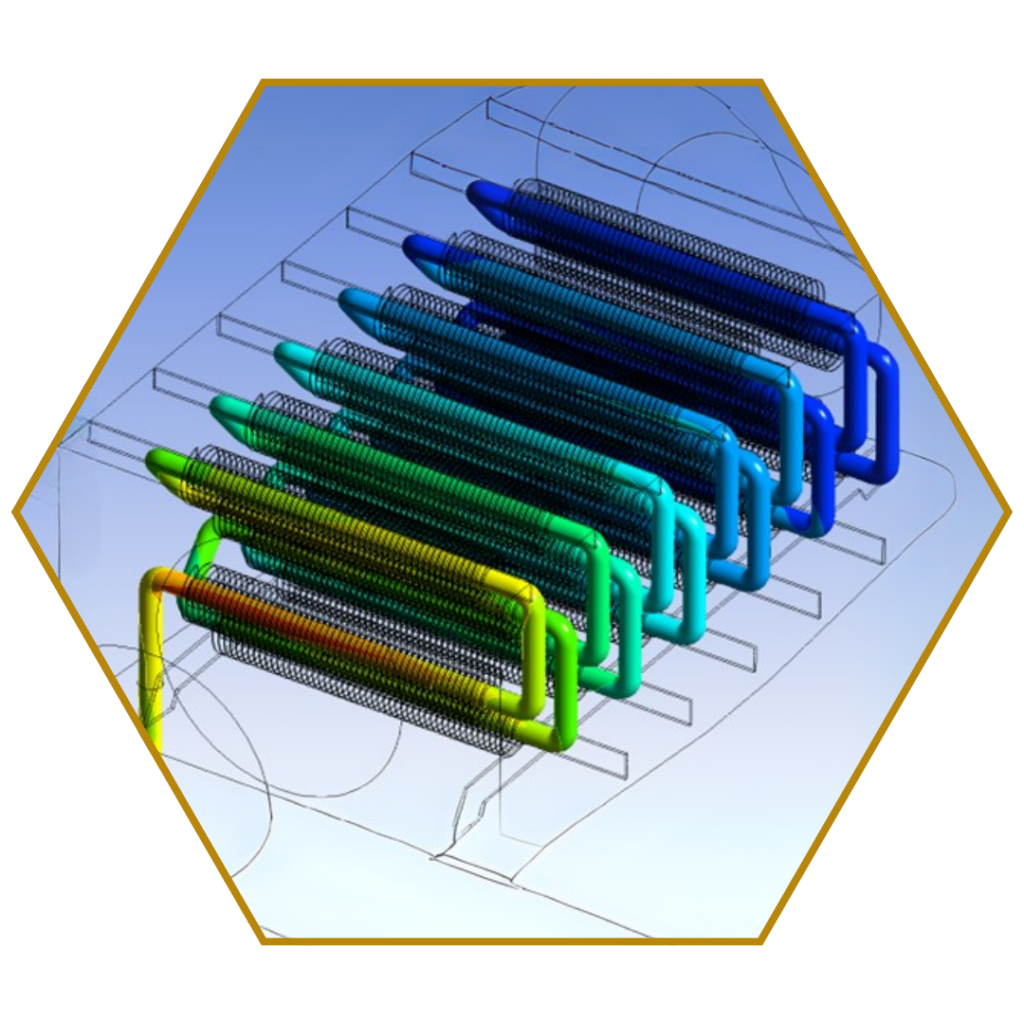
To achieve industry-leading performance, it has become essential to leverage the knowledge of modern high-performance computing methods available at the National Competence Centre in High Performance Computing (HPC).
Flue gas cooling is a technological challenge
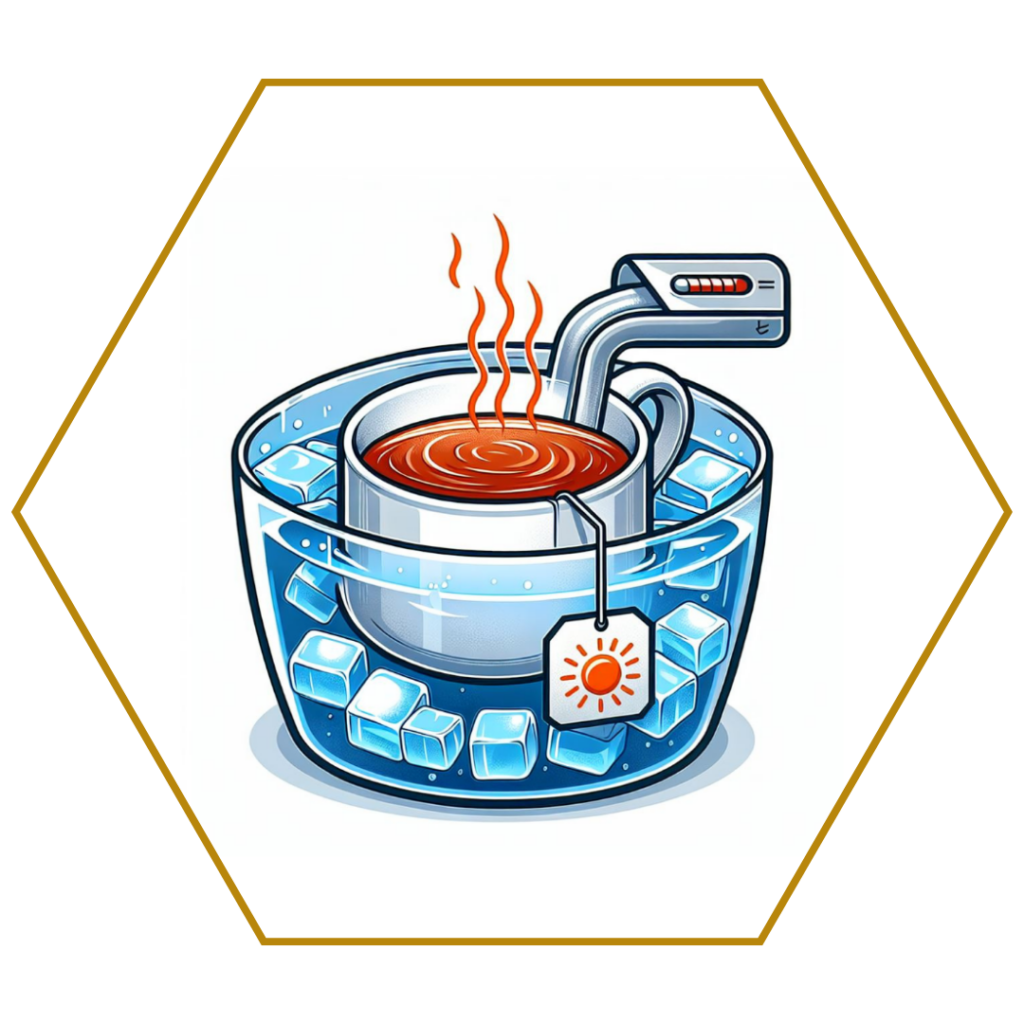
“A heat exchanger works similarly to a cup of hot tea placed in ice-cold water – the heat passes through the wall of the cup into a cooler environment,” explains Tomas Karasek, Head of the National Competence Centre (NCC) in High-Performance Computing (HPC).
The heat exchanger developed by HEGAs works similarly. However, it replaces the cold water in the pipes with refrigerant, which removes the so-called low potential heat from the flue gases (gases produced during fuel combustion), which would no longer be used and go up the chimney as warm flue gases. This heat is then used to generate electricity.
Therefore, developers work with a large number of variables and require immediate feedback on the consequences of optimising key parameters. These can include flow rates, heat losses, and material properties. However, knowledge of thermal performance is critical.
Numerical modelling and simulation can be the solution
The experts of IT4Innovations National Supercomputing Center, which also serves as the National Competence Centre in HPC for the Czech Republic, thoroughly analysed the existing designs and methods with the consortium representatives in initial consultations. They also saw an opportunity to solve their challenges through numerical modelling and simulation.
Numerical modelling provides key advantages in developing the exchanger and, in particular, enables:
- faster and cheaper development by minimising physical prototypes,
- accurate simulation of heat transfer or fluid flow,
- prediction of potential failures.
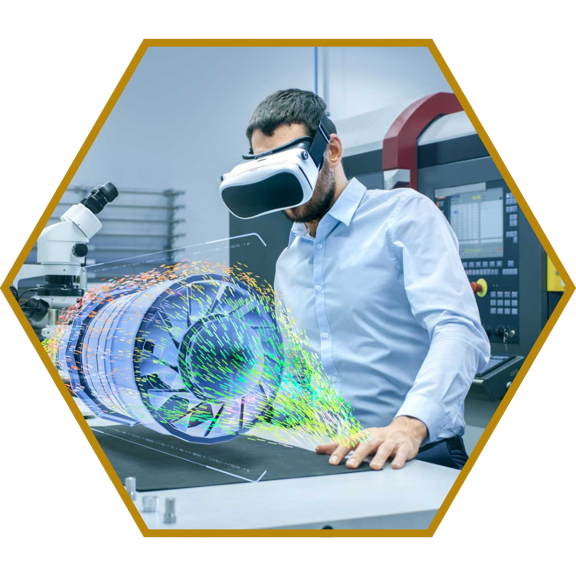
It also provides a detailed understanding of the system’s behaviour under different operating conditions, leading to optimised design, increased efficiency, and improved equipment reliability.
It also reduces energy losses, extends exchanger life, and customises the design to specific requirements, giving companies a significant competitive advantage in the marketplace.
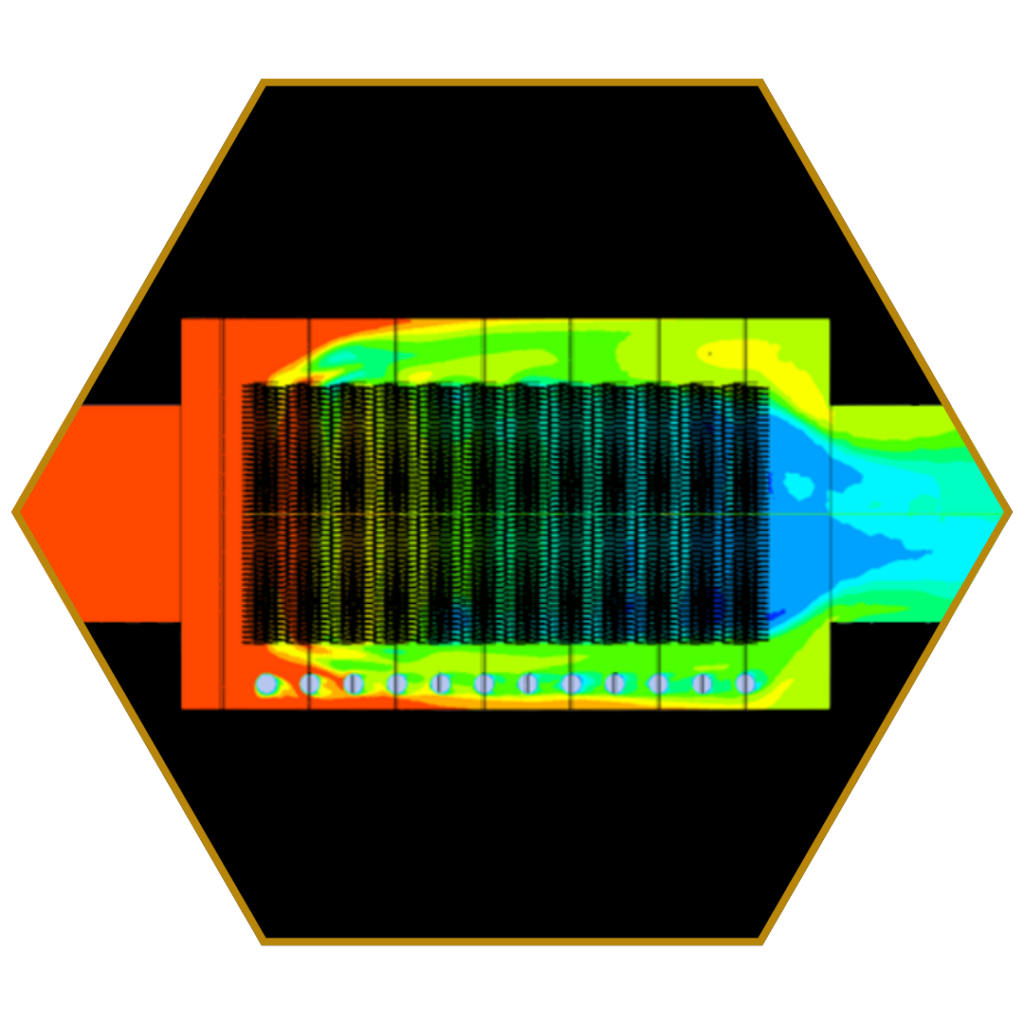
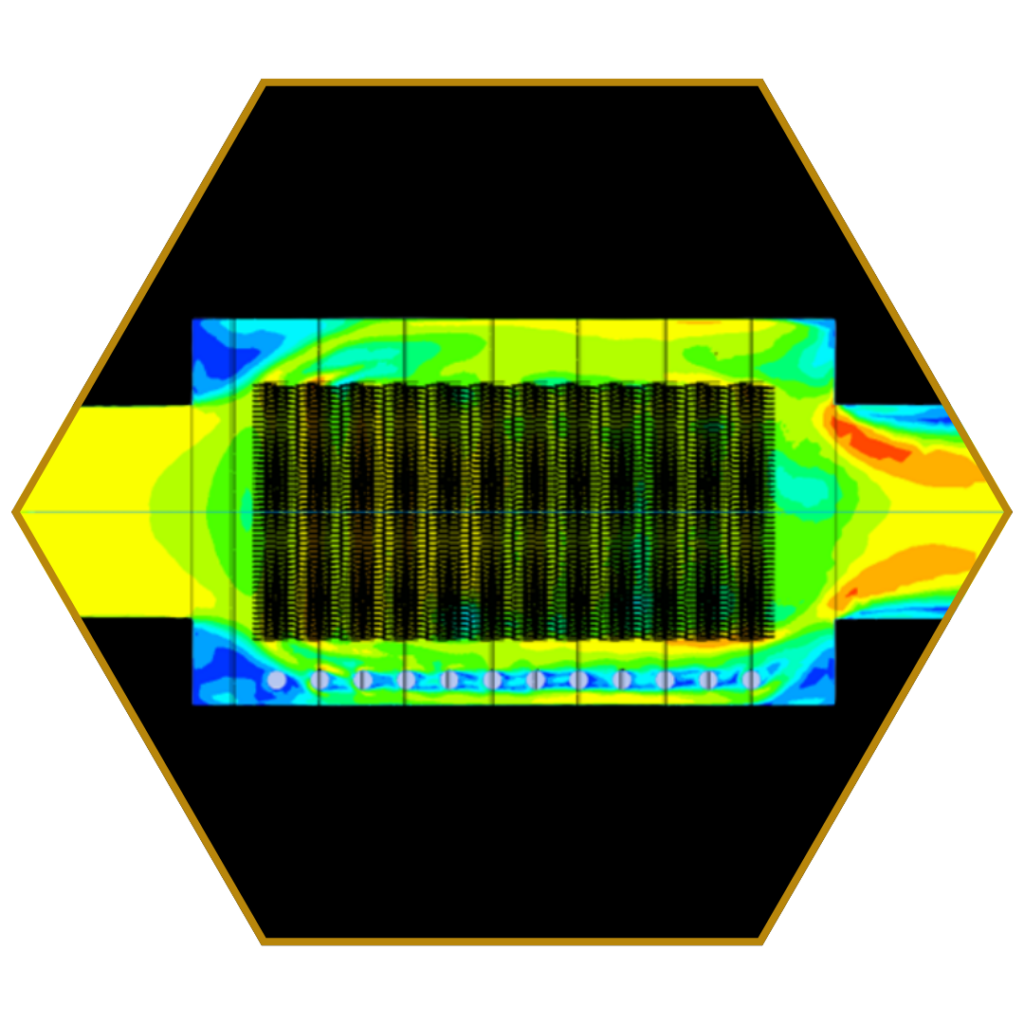
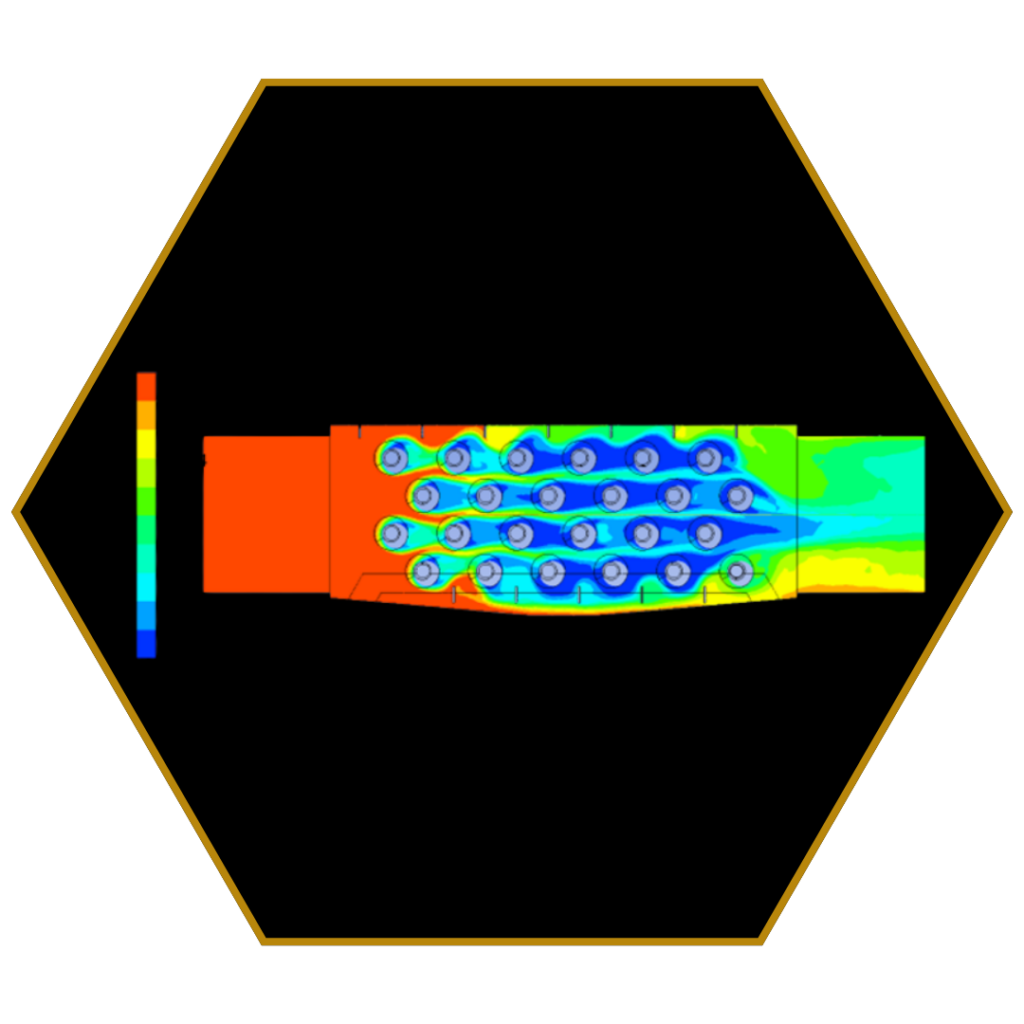
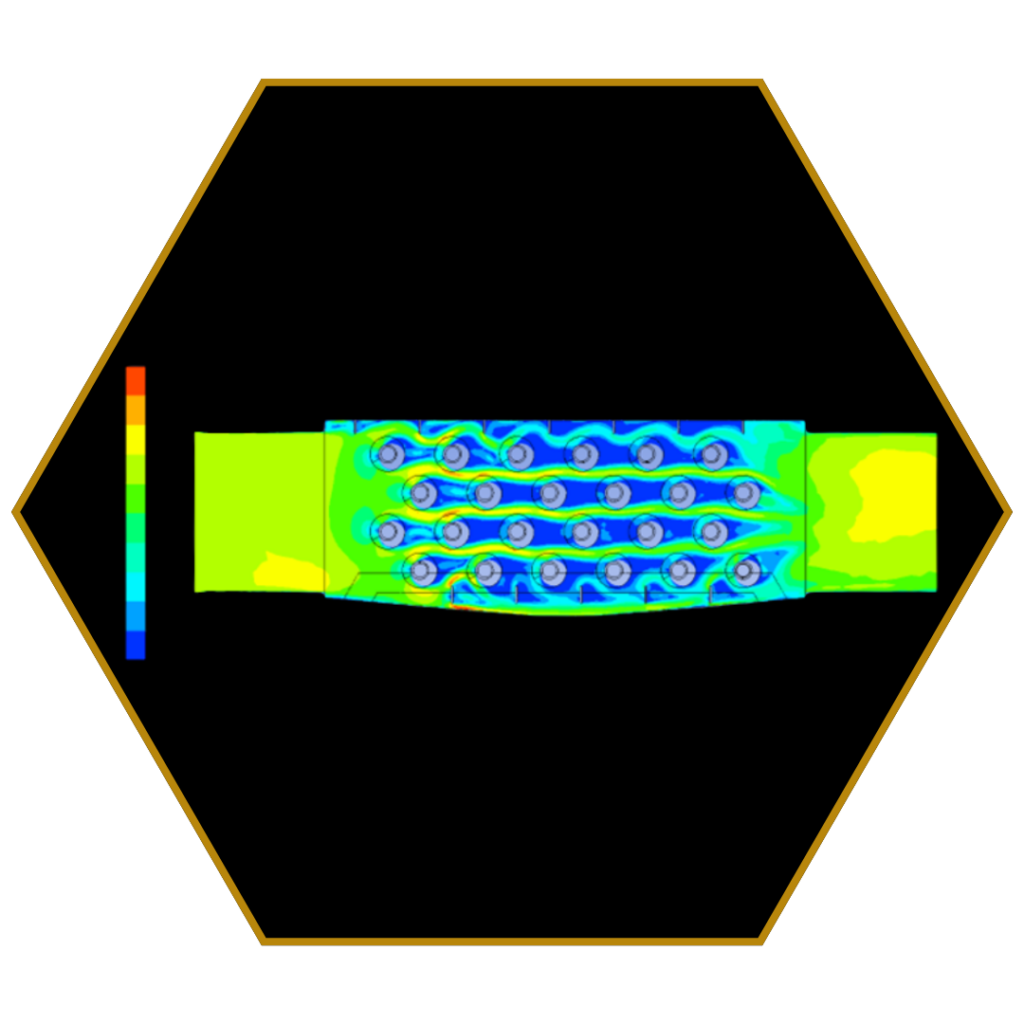
Result: faster and cheaper development and detailed information about ongoing processes
The cooperation with IT4Innovations has given HEGAs not only a technical solution but also a new perspective on the possibilities of their product development. By using numerical modelling and supercomputer simulations, they have overcome the limits of traditional design methods and opened the door to more efficient and sustainable manufacturing. This collaboration is a prime example of how connecting scientific capabilities and industry can lead to innovation with real market impact.
Ing. Jan Koloničný, Ph.D. on cooperation:
Centre for Energy and Environmental Technologies
“Exchanger design is one of the basic activities for our company because exchangers of different types are an integral part of all power units.
Personally, I was surprised by the results that can be achieved using modern computational methods. These simulations have allowed us to look inside the heat exchanger itself and thus obtain information about the flue gas flow around the heat exchanger surfaces.
The existing methods work with efficiencies that can only be estimated more or less accurately based on previous experience. This then means that the heat exchanger is often oversized.
The simulations have contributed significantly to the design and optimisation process, allowing us to better understand the internal processes and to determine the heat exchange efficiency more accurately.”
Read about more successful collaborations.
Don’t miss any news. Follow NCC Czechia on social media.